HIO Steam flaking mills
One HIO Steam flaking mills Capacity from 200-240tpd
Configration
1、The flaker shell ,protective cover , front and rear, upper and lower door panels of the steam corn flaker are made of all stainless steel plates, and the parts in contact with the material are SS304 stainless steel
2、Equipped with SKF bearing, SEW geared motor, Siemens Barde high-efficiency and energy-saving motor; equipped with steam exhaust device to reduce the corrosion of steam to equipment;
3、Energy-saving PLC hydraulic pump station, all control speed regulation and splitting rolls can
be controlled by the pump station;
4、Adopt China First Heavy Industry's high nickel-chromium-molybdenum alloy roll, centrifugal composite casting, hardness HS73±3, after dynamic balance test, the thickness of the alloy layer is 30-35mm, and one wire drawing can process 35,000-45,000 tons of corn flakes;
5、Equipped with a magnetic separation mechanism to prevent damage to the rolls by iron in the material; fully enclosed design, safe and beautiful;
6、The pulley is designed with a tensioning sleeve, and the bearing does not need to be damaged when disassembling the roller, and the pulley adopts the CPT brand;
Accessories: host × 1; motor × 1; motor slideway × 1; transmission belt × 4; stainless steel feeding hopper × 1; manual × 1
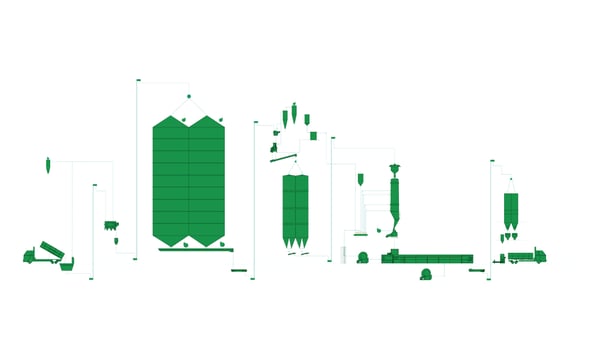
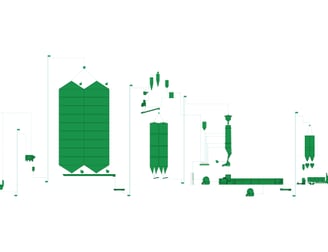
Application
The material that can be processed by the production line
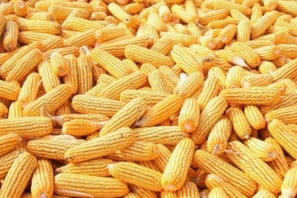
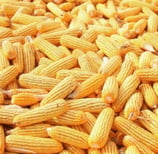
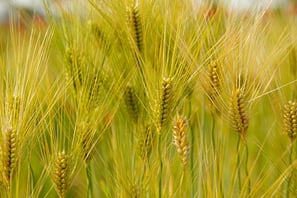
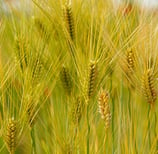
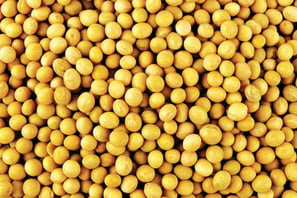
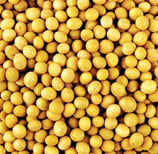
Corn
Barley
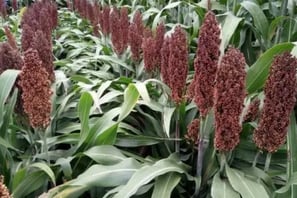
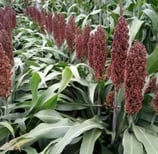
Sorghum
Soybean
Application scope of corn flakes


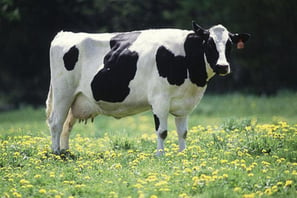
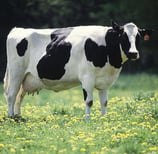
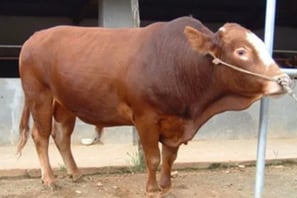
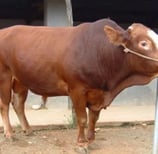
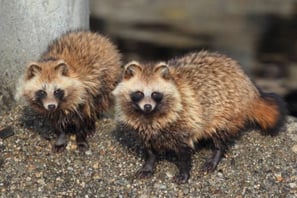
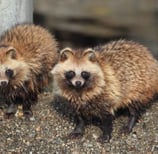
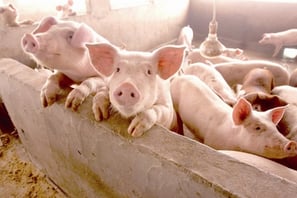
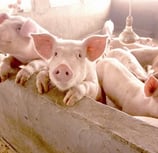
Cow feed
Beef cattle feed
Suckling pig feed
Fox and raccoon feed
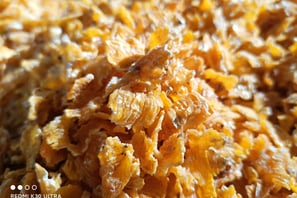
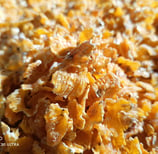
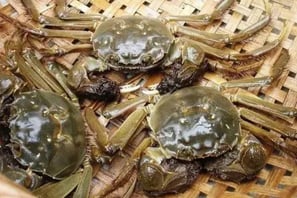
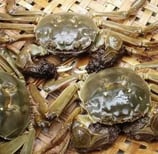
Substitute for crushed corn feed
Crab feed
Process Overview
All equipment of the standard process production line
See the equipment list for details.
Optional equipment:
Raw material steel silo
Moistening system
Air compression system
Steam boiler
Steam piping and valves in the workshop
Equipment insulation
Automatic traction sewing and packaging system
Automatic palletizing system
Condensate recovery system
Bulk warehouse for finished products
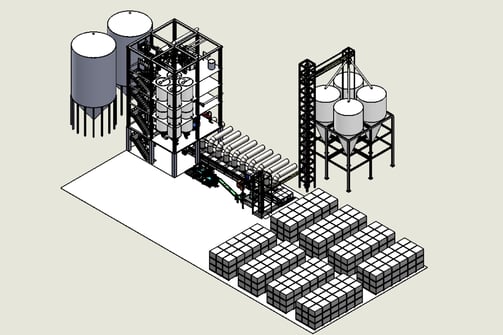
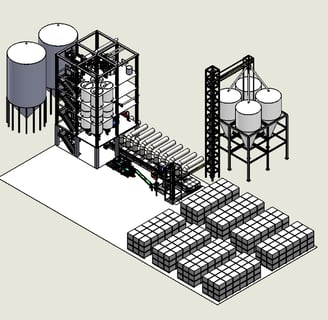
Feature 1 - Zero steam leakage
Zero steam leakage:
1.The main equipment of the Grosper production line all uses German EMKA sealing strips;
2.Good sealing effect and longer service life;
3.The main unit is equipped with a steam recovery device, and the moisture-absorbing fan discharges the steam to the outside;
4.Avoid equipment corrosion in the workshop;
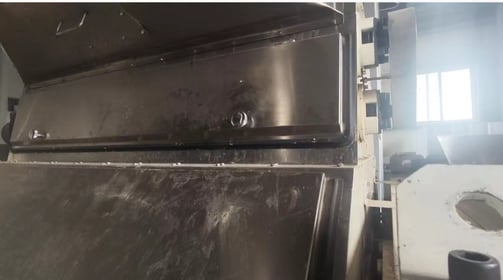
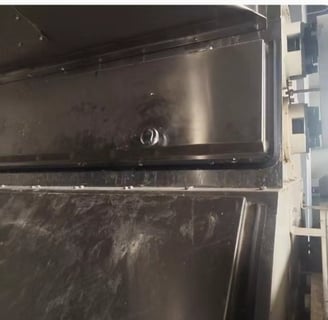


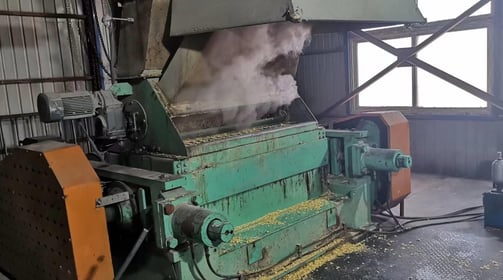
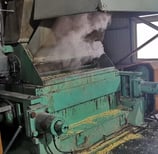
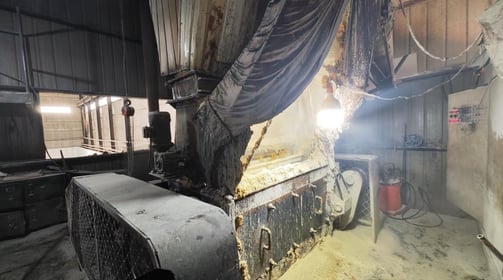
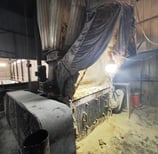
Other manufacturers
Other manufacturers
Feature 2 - High stability
1.Reasonable process design
2.All equipment is made of genuine materials
3.High stability of the automatic control system
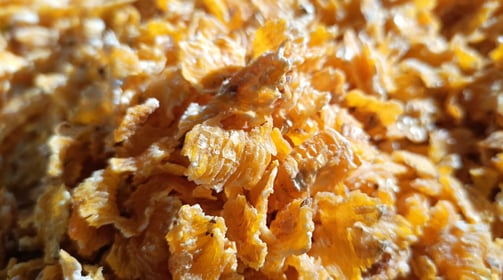
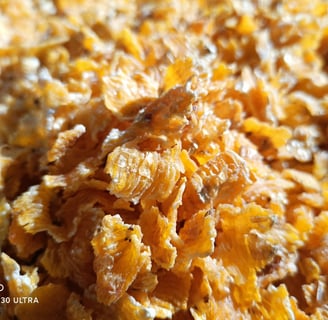


Grosper provides efficient and reliable equipment to ensure feed/food safety and production efficiency;
Grosper focuses on how to improve productivity and equipment efficiency;
The FC series pellet mill can achieve a maximum single drawing of 65,000 tons;
The longest non-stop production of the production line is 55 days.
Configuration list:
1.1 Output: 240 tons/24 hours, corn;
1.2 Flake thickness: 1.2-2.0mm (adjustable);
1.3 Weight: 16.7 tonsFeeding unit:
2.1 Equalizing feeder, SS304 stainless steel feeding roller;
2.2 Mixing device, stainless steel bearings;
2.3 Reducer: SEW hard-tooth surface reducer, 1.1kw*1;
2.4 Built-in scraper technology, detachable and adjustable, to remove adhered materials from the roller;
2.5 Hydraulic system: PLC fully automatic hydraulic pump station, 2.2kw;
2.6 High-pressure pressure-resistant hose.
2.7 Motor: Domestic motor, 110kw×1;Basic unit:
3.1 No. 45 steel welded base, through high-temperature annealing process, stable structure;
3.2 Fully enclosed structure, German EMKA high-temperature resistant sealing strips, steam recovery device;
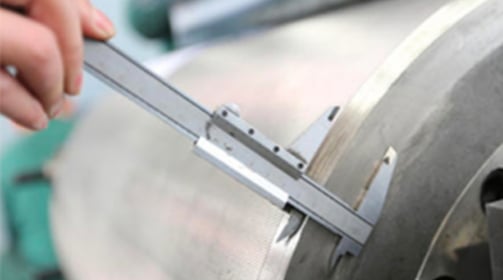
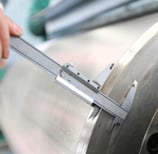
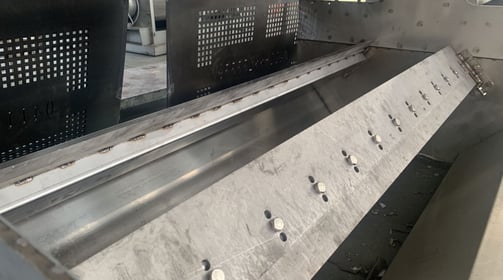
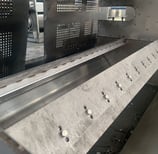
Roll
Scraper system
Flaking unit:
4.1. Hydraulic roll tightening, using square bearing tile seats and equipped with wear-resistant sliders;
4.2. All SS34 stainless steel contact material parts;
4.3. Equipped with bearing temperature monitoring system to monitor the temperature of the roller bearings at any time;
4.4. Online adjustment of the thickness of the embryo sheet without stopping the machine and splitting the rollers; slider gap微调 adjustment technology;
4.5. Shoulder baffle anti-leakage device;
4.6. Rolls: High-nickel-chromium-molybdenum alloy rolls blank from China First Heavy Industries, with a thickness of 35-40mm for the alloy layer; exclusive drawing process by Gaochang; 45# forged roll shaft head
4.7. Bearings: Grosper high-temperature-resistant bearings; the bearings adopt a push sleeve structure for easy disassembly and assembly;
4.8. Automatic lubrication and refueling system;
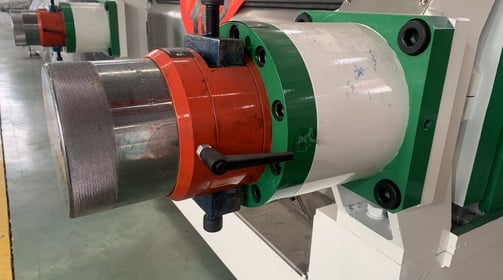
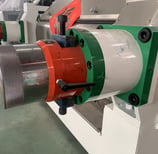

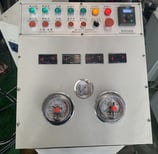
High-efficiency hydraulic pump station
Slider type clearance fine-tuning device
Feature 2 - High stability - HDC drying and cooling system
Head and tail boxes: Made of 8mm carbon steel.
Box: 2.5mm aluminum-zinc-coated steel plate produced by laser numerical control;
Equipped with observation windows, maintenance doors, and hand holes;
Temperature sensor: PT100;
Equipped with uniform turning material system;
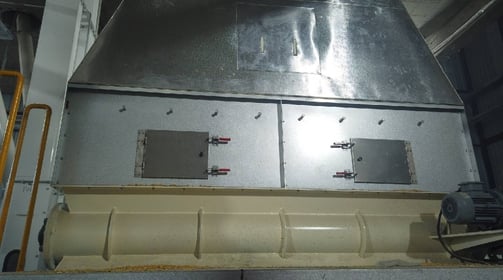
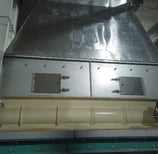
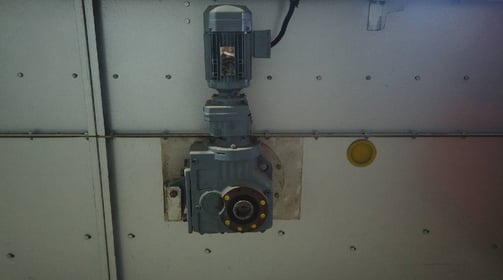
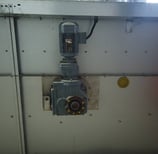
Rotating fabric system+material distribution
Material flipping
6. Guomao hard tooth surface reducer: 0.75kw*1
7. Bottom ventilation: 1.5mm 201 stainless steel one-time stamping forming;
8. Dry evenly without leakage;
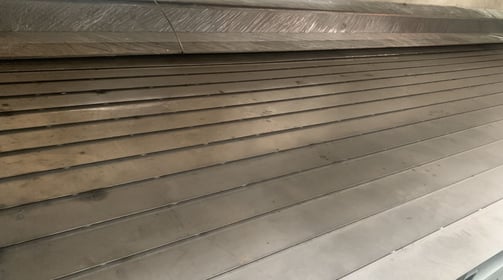
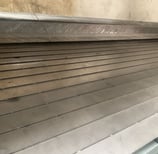
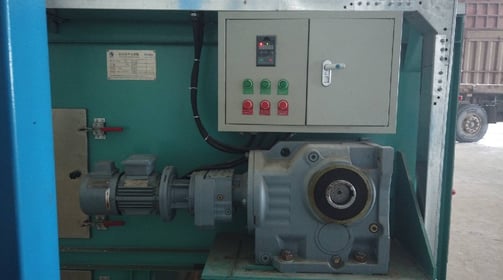
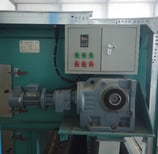
Guomao hard tooth surface reducer
Bottom ventilation
Chain: 304 stainless steel material;
Square tube: Galvanized steel pipe material;
Level switch: 90 brand;
Design condensate centralized drainage system;
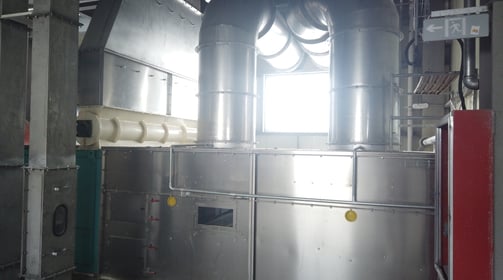
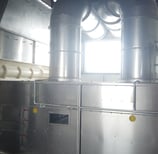
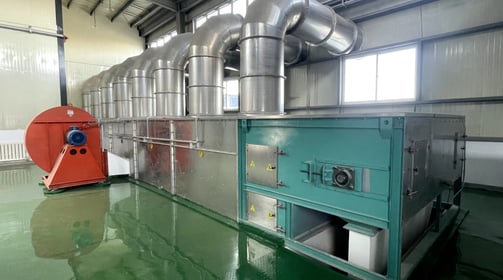
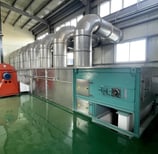
Bottom ventilation
Condensate drainage system
Feature 2 - High stability - Supporting equipment with genuine materials
Cleaning equipment Zhongliang Kaifeng Maosheng or Bühler...
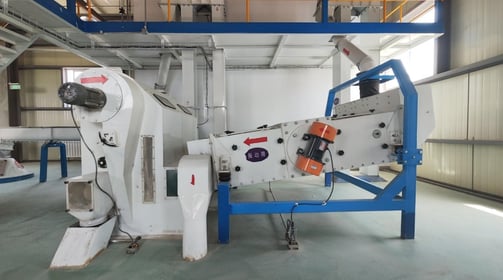
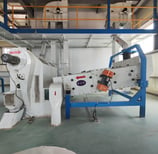
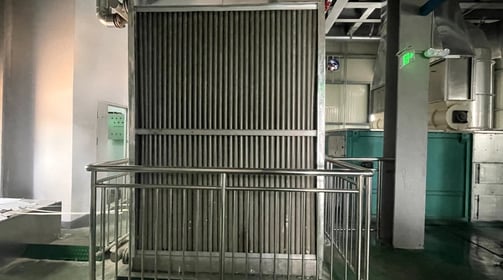
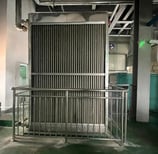
Photos of cleaning equipment
Photos of heat exchangers
Clamp-type chute, the conveying material section adopts a double-layer for more wear resistance.
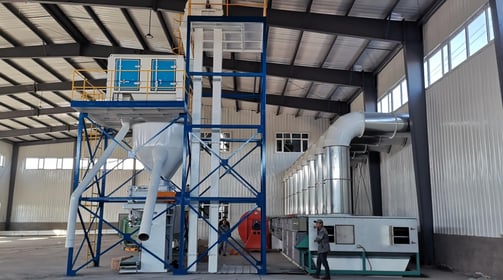
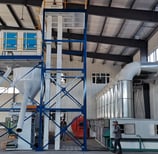
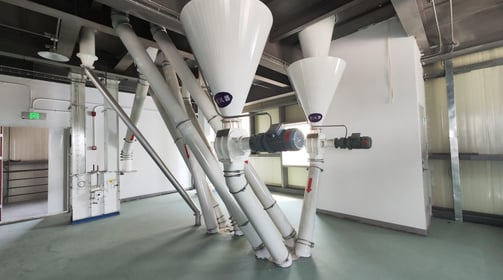
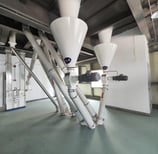
Clamp-type chute
Maintenance platform
Heat exchanger aluminum fins (optional 304 stainless steel)
Standardized maintenance platform
Feature 3 - High quality of finished corn flake products
Powder degree is low
Degree of gelatinization
Prevent mildew and caking
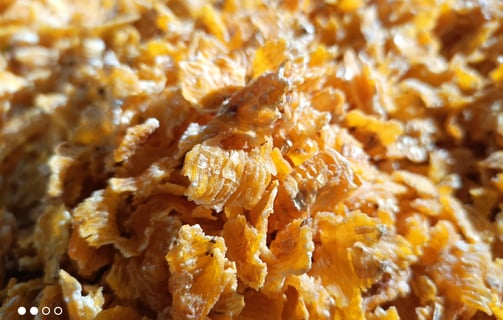
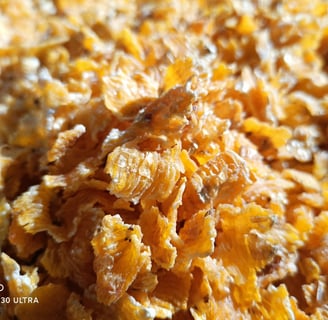
The design is reasonable, and more gravity flow is used to reduce the use of conveying equipment.
All conveying equipment uses slow speed anti-breaking to reduce material fragmentation.
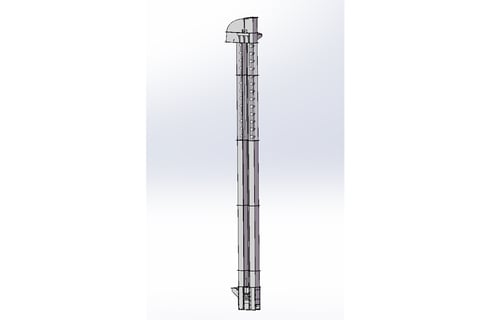
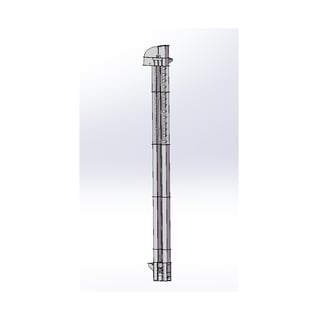
The equipment has a total of 6 layers of steam balancing devices, which can ensure that the steam is evenly distributed inside the conditioning tower to achieve the effect of uniform conditioning. The steam and corn move in the opposite direction, so that the material is gradually conditioned from bottom to top. After about 1 hour of cooking, the moisture content of the corn can be increased from 16-18% at the original inlet to 18-20% at the outlet, and the degree of gelatinization can be adjusted to 65-80%. The temperature of the corn can also be raised to 100°C at the same time.
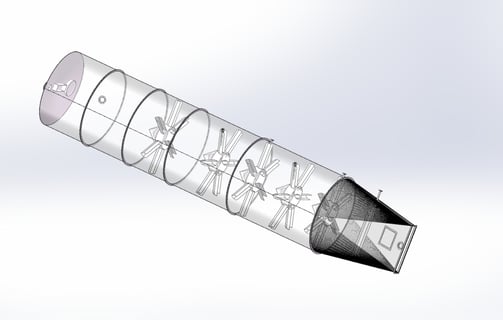
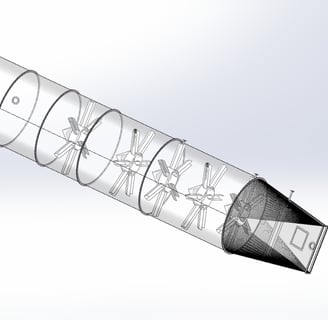
Fully computerized control system and manual control system can be converted to each other;
Electrical configuration: The main component PLC control module uses Siemens brand. Electrical components are all adopting Chint;
For single motor above 55kw, soft start is used, and for below 15kw, direct start is used;
The entire set of engineering only requires one person to operate, which is clear at a glance;
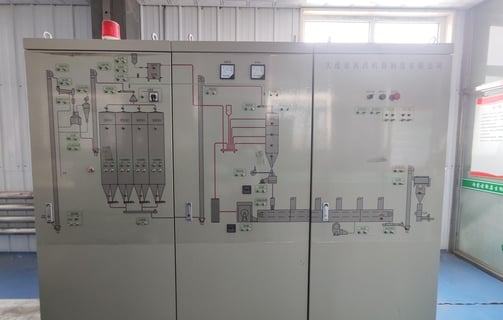
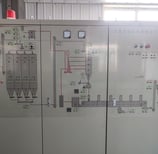
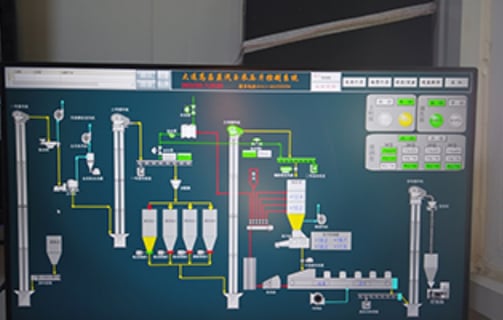
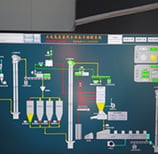
Three sets of distribution cabinets
Monitor home page
Choosing our advantages
Under the evaluation system of YouRan supplier, more than 70% of the top 20 customers of Gaochang are customers served by Dalian Gaochang.
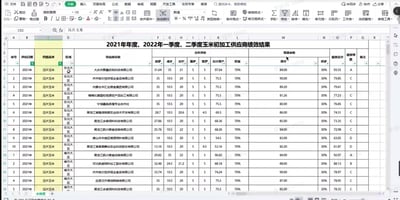
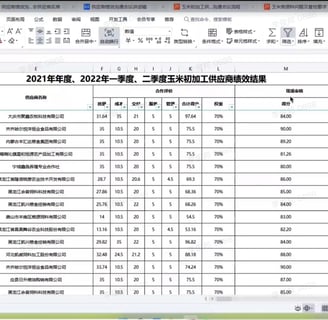
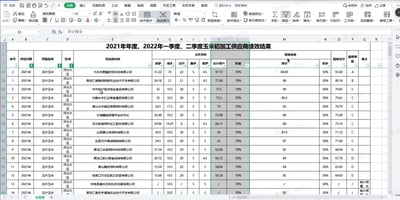
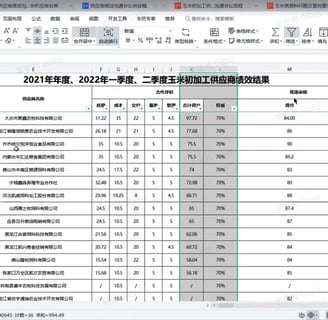
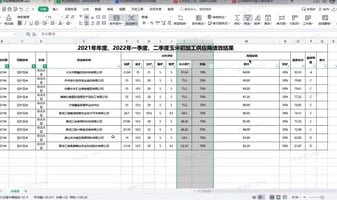
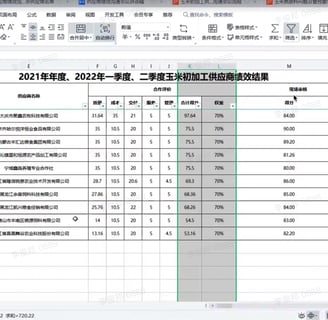
Grosper Corn Flaking Project Case
More than 80 domestic high-end customers choose Dalian Gaochang.
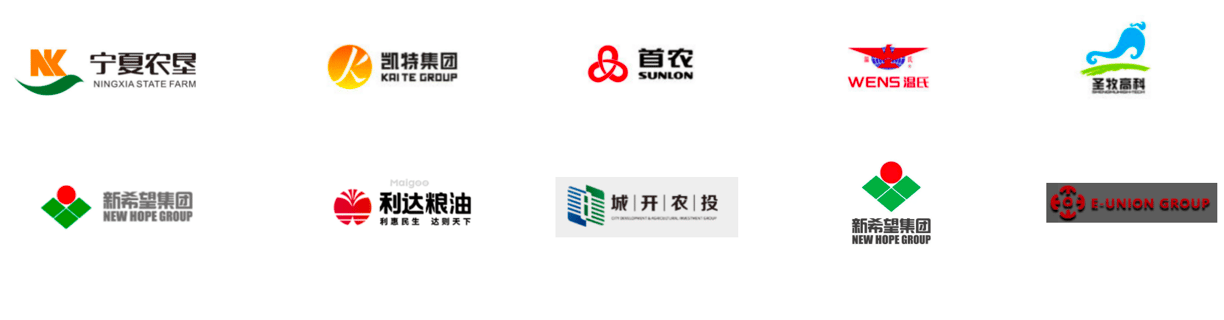
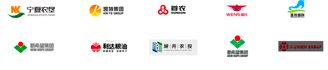
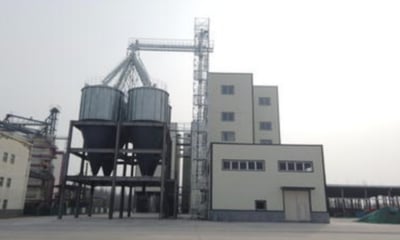
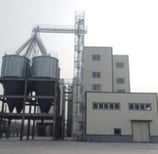


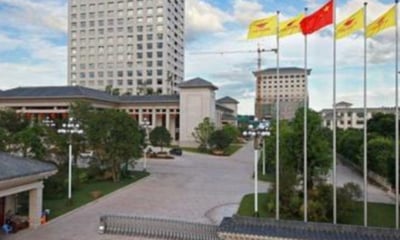
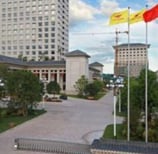
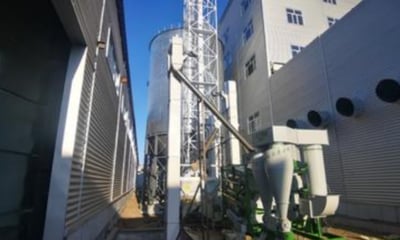
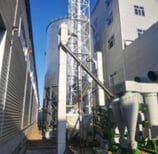
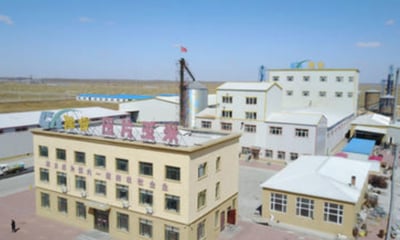
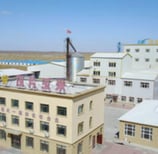
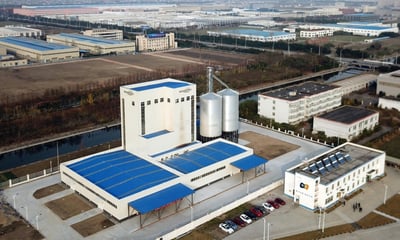
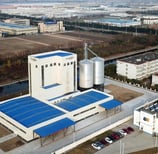
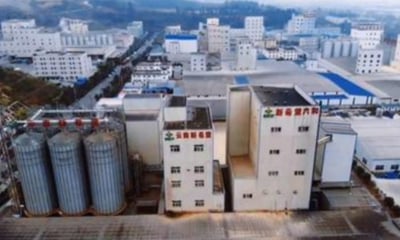
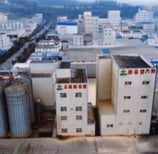
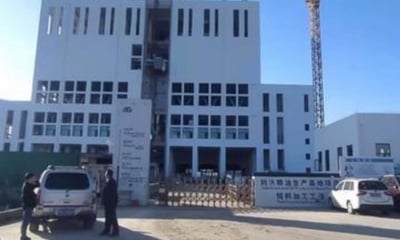
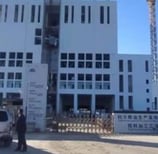
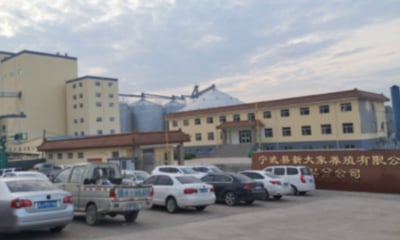
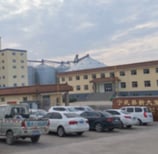
Basic Configration:
It adopts fully enclosed structure, with cooling nets on both sides, square bearing seat , front and rear door panels can be opened, easy to clean, and there are observation ports on both sides of the bottom to facilitate the observation of material effects.
Daliy Output:
200-220tons/24 hours (subject to the corn after tempering and softening)
Roller:
Adopt China First Heavy Industry's high nickel-chromium-molybdenum alloy roll, centrifugal composite casting, hardness HS73±3, after dynamic balance test, the thickness of the alloy layer is 30-35mm
Motor:
Single driven motor,110KW
Recuder
Brand:SEW
Bearing
Brand:SKF
Shell
The flaker shell ,protective cover and front and rear upper and lower door panels of the steam corn flaker are made of all stainless steel plates, and the parts in contact with the material are SS304 stainless steel
Pully
Brand:CPT
Hydraulic System
PLC hydraulic pump station. The hydraulic pipe adopts high pressure and pressure resistant oil pipe, power: 2.2kw.
Equipment Base
45 gauge steel welded base, after annealing treatment, the structure is stable and not easy to deform.
Tight Roller Method
Hydraulic tightening roller ,adopts square bearing seat.The front hydraulic pressure is equipped with a dial adjustment and locking device, which can adjust the thickness of the flakes online without the need for pressure relief and shutdown. The operation is convenient and reliable, saving time and labor, and saving labor costs.
Anti-leakage Device
Anti-leakage material for shoulder baffles.
Scraper System
It is convenient to clean the material attached to the roll, and the scraper can be replaced and adjusted.
CORE ADVANTAGES
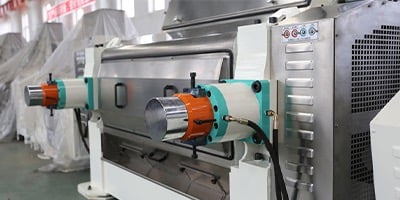
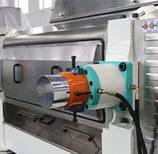
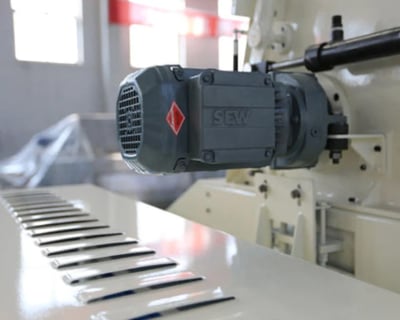
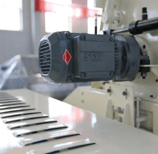
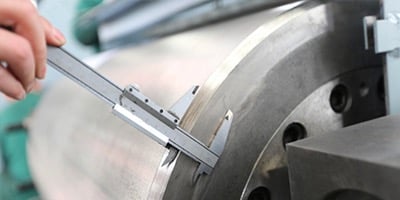
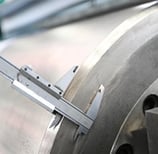
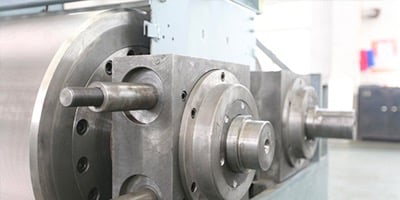
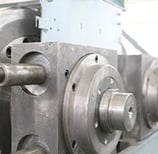
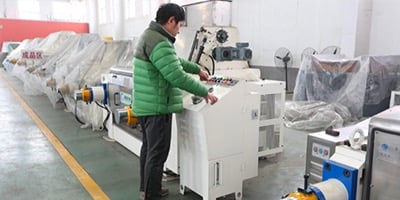
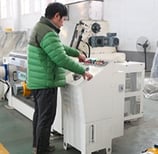
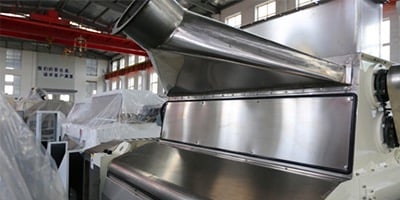
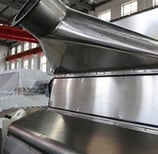
Hydraulic Dial
Adjust the thickness of the flakes online without the need for pressure relief and shutdown.
Easy to use
SEW Reducer
Meet high-intensity production needs.
International brand
Grosper Roller
German WALZENIRLE centrifugal compound
casting process one time drawing can press more
than 45,000 tons
Square tight roller stabilization system suitable for high
pressure flaking needs
Fully automatic PLC hydraulic control system.Easy to operate, fully computer controlled
Feeding speed regulation, online adjustment of flakes thickness
Whole Closed Structure
Maximum prevention of steam escapeEquipped with special exhaust device
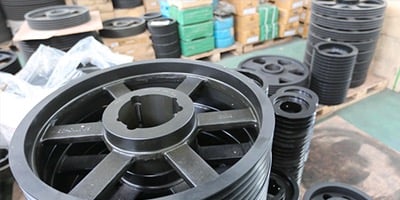
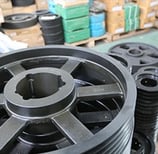
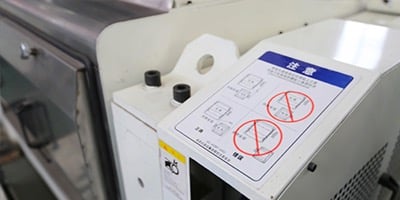
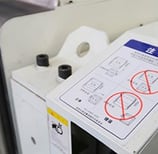
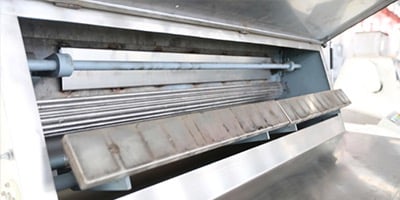
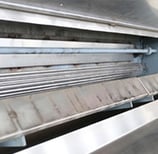
CPT drive system
Strong stability, customized by Grosper
EU standard warning signs
Safe production, be prepared
Magnetic separation system
Prevent metal damage to rolls